Planning a new warehouse project but unsure about the associated costs? On average, it can cost around $20 per square foot to build a warehouse. This comprehensive guide will help you understand all the factors that might affect your budget, from design and material choices to location considerations.
Dive in, untangle potential construction expenses and deliver your future warehouse project on time and within budget!
Key Takeaways
- The average cost to build a warehouse is around $20 per square foot.
- Factors such as size, type, design, materials, location, and use case can affect the overall construction costs.
- The phases of warehouse construction include initiation, pre-construction, procurement, construction stage, and post-construction.
- Controlling warehouse construction costs can be achieved through efficient design choices like utilizing natural light and implementing voice-enabling technology.
Factors Affecting Warehouse Construction Costs
The size and square footage, type of warehouse, design costs, material costs, location, and use case all play a significant role in determining the overall cost of building a warehouse.
Size and square footage
The size of your warehouse matters a lot. Bigger warehouses cost more to build. If you plan to make a small 1200 square foot warehouse, it may cost around $25,000. A larger 50,000 square foot one can range between $600,000 and $950,000.
The price per square foot often falls around $20. But always check your city’s rates as they can change from place to place.
Type of warehouse
There are different types of warehouses, and the type you choose can impact the cost of construction. A basic warehouse shell typically costs around $20 per square foot. However, if you want a steel warehouse or a distribution center, the cost can vary.
For example, a 50,000 to 60,000 square foot distribution center can range from $600,000 to $950,000 to build. The specific type of warehouse you need will determine the materials and features required, which in turn affects the overall cost.
So when estimating your warehouse construction expenses, consider the type of warehouse that suits your needs and budget.
Design costs
The design of a warehouse is an important factor that can affect the overall construction costs. The complexity and aesthetic features of the design can increase the expenses. Additionally, if you want to include specialized systems or technologies, it may further add to the cost.
Remember that sophisticated designs and intricate structures often require more materials and labor, resulting in higher prices for building a warehouse. So, when planning your budget, consider these design costs alongside other factors like size and location.
Material costs
The cost of materials is an important factor in determining the overall cost of building a warehouse. The type and quality of materials used can greatly impact the final price. For example, the average cost for building a warehouse shell is $20 per square foot.
However, additional material costs for sophisticated systems or aesthetically complex designs can increase the price to over $100 per square foot. It’s also important to consider factors such as concrete flooring options and the complexity of the project when estimating material costs.
Ultimately, it’s crucial to check specific prices for the city where construction will take place to get an accurate estimate.
Location
The location of the warehouse plays a significant role in determining its construction costs. Depending on the city and region, prices for land, permits, labor, and materials can vary greatly.
For example, building a warehouse in a metropolitan area will likely be more expensive compared to a rural area. It’s important to research specific prices for the city where you plan to build your warehouse to get an accurate estimate of the costs involved.
Use case
When considering the cost of building a warehouse, one important factor to consider is the specific use case for the facility. Different types of warehouses will have different requirements and therefore, varying costs.
For example, if you plan to use the warehouse as a distribution center for perishable goods, you may need specialized refrigeration systems, which can increase construction costs. On the other hand, if you only need a small warehouse for storing non-perishable items, your expenses may be lower.
Understanding your specific use case and its unique requirements will help you estimate and control construction costs more effectively.
Phases of Warehouse Construction
The phases of warehouse construction include initiation, pre-construction, procurement, construction stage, and post-construction.
Initiation
Warehouse construction begins with the initiation phase. During this phase, the project is planned and organized. It involves conducting feasibility studies to determine if building a warehouse is viable based on factors such as location, cost, and resources.
The budget for the construction is also established during this stage, taking into account factors like size and square footage of the warehouse. Additionally, permits and approvals are obtained to ensure that all legal requirements are met before starting the construction process.
Overall, the initiation phase sets the foundation for a successful warehouse construction project by carefully considering all aspects of planning and preparation.
Overall: When initiating a warehouse construction project, careful planning is necessary to consider factors such as feasibility, budgeting, permits/approvals.
Main points:
1. Initiation phase involves feasibility studies to determine viability.
Pre-construction
Before the actual construction begins, there is a phase called pre-construction. During this phase, important steps are taken to prepare for the construction of the warehouse. This includes activities like obtaining permits and approvals, conducting site surveys and soil testing, creating detailed plans and designs, estimating costs, and securing financing if needed.
Pre-construction also involves hiring contractors or builders and scheduling the construction timeline. It is crucial to carefully plan and prepare during this phase to ensure a smooth construction process while keeping costs under control.
Procurement
During the procurement phase of warehouse construction, it is important to carefully choose the materials and equipment needed for the project. This includes sourcing suppliers for steel, concrete, insulation, roofing materials, and more.
By comparing prices from different vendors and negotiating contracts, you can ensure that you get the best value for your money. It’s also crucial to consider quality when procuring materials – cheaper options might save you money upfront but could result in higher maintenance costs in the long run.
Another aspect of procurement is obtaining the necessary permits and approvals from local authorities. This involves submitting plans and documents to relevant departments and paying any required fees.
It’s important to factor in these costs when estimating the overall budget for warehouse construction.
Moreover, during this phase, it is advisable to engage with professional contractors who have experience in warehouse construction projects. Requesting multiple quotes from different contractors will allow you to compare prices while considering their expertise and track record.
Construction stage
During the construction stage of a warehouse, the actual building process takes place. This involves activities like laying the foundation, erecting the walls and roof, installing utilities such as plumbing and electricity, and completing interior finishes.
The cost of this stage can vary depending on factors like the size of the warehouse, materials used, labor costs, and any additional features or customization required. It is important to carefully consider these factors to ensure that the construction stays within budget.
Post-construction
After the construction of a warehouse is complete, there are still some important things to consider. One key aspect is maintaining the building and ensuring it remains in good condition.
This includes regular inspections, repairs, and maintenance work to keep everything functioning properly. Another consideration is optimizing the space within the warehouse for efficient operations.
This can involve organizing shelving and storage systems, implementing automation technologies, and making sure the layout supports smooth workflows. Additionally, it’s important to factor in ongoing costs such as utilities and insurance when budgeting for post-construction expenses.
Controlling Warehouse Construction Costs
Implementing cross docking can help reduce warehouse construction costs by streamlining the flow of goods and minimizing handling and storage requirements.
Use of natural light
Natural light is a cost-effective way to illuminate a warehouse. It can significantly reduce electricity usage and lower energy costs. By incorporating windows, skylights, or translucent panels in the building design, natural light can be maximized.
This helps create a brighter and more comfortable working environment for employees while also reducing the need for artificial lighting during daylight hours. Plus, studies have shown that exposure to natural light improves productivity and overall well-being among workers.
So by utilizing natural light, not only will you save money on utility bills but also create a better workspace for your employees.
Voice-enabling technology
Voice-enabling technology is an innovative solution that can help control warehouse construction costs. By integrating voice-controlled systems, you can improve efficiency and reduce labor costs.
With this technology, workers can receive instructions and updates through a hands-free device, allowing them to work faster and with fewer errors. Voice-enabled picking systems can also optimize the use of space in the warehouse, leading to better inventory management.
Implementing voice-enabling technology may require an initial investment, but it can ultimately save money by improving productivity and streamlining operations in your warehouse facility.
Implementing cross docking
Cross docking is a cost-effective strategy that can help reduce warehouse construction costs. With cross docking, incoming shipments are unloaded from trucks and immediately loaded onto outbound vehicles.
This eliminates the need for long-term storage in the warehouse, saving space and reducing handling costs. By implementing cross docking in your warehouse design, you can optimize your space utilization and potentially lower your overall construction expenses.
Pest control measures
Pest control is an important aspect of warehouse construction that can affect costs. By implementing effective pest control measures, you can prevent damage to inventory and minimize the need for expensive repairs.
These measures include regular inspections, sealing cracks and gaps, installing screens on windows and doors, using pesticides when necessary, and maintaining cleanliness inside the warehouse.
Taking these precautions can help you save money in the long run by avoiding costly infestations or damage caused by pests.
Limited use of concrete tilt-up wall or steel
Concrete tilt-up walls and steel are commonly used in warehouse construction, but limiting their use can help reduce costs. Instead, alternative materials or methods can be considered to achieve cost savings.
For example, using pre-engineered metal buildings or utilizing other types of wall systems such as insulated metal panels can provide a more affordable option. By exploring these alternatives and considering the specific needs of the warehouse project, cost-conscious buyers can find ways to minimize expenses while still ensuring a structurally sound and functional building.
Efficient design for optimized space utilization
Efficient design is important when building a warehouse because it helps to maximize space utilization and reduce costs. By carefully planning the layout and organization of the warehouse, you can ensure that every inch of space is used effectively.
This means considering factors such as storage systems, equipment placement, aisle width, and traffic flow. Incorporating features like mezzanines or vertical racking can also help to make use of vertical space.
An efficient design will not only save money by minimizing wasted space but will also improve productivity by making it easier for workers to find and retrieve items quickly.
Timeframe for Warehouse Construction
Factors such as site preparation, design complexity, and permitting can impact the timeline for warehouse construction. Read on to discover the average timeframe for building a warehouse and factors that influence the construction timeline.
Factors influencing construction timeline
The construction timeline for a warehouse can be influenced by various factors. These include:
- Size of the warehouse: Larger warehouses generally take longer to construct compared to smaller ones.
- Complexity of the design: A warehouse with unique architectural features or complex layout may require more time for construction.
- Site preparation: Clearing the land, leveling, and preparing the site can impact the overall timeline.
- Permitting and approvals: Obtaining necessary permits and approvals from local authorities can cause delays in the construction process.
- Availability of labor and materials: Shortages in skilled labor or building materials can slow down the construction timeline.
- Weather conditions: Adverse weather such as heavy rain, snowstorms, or extreme temperatures can delay construction work.
- Unforeseen issues: Unexpected challenges like soil conditions, structural problems, or utility connections can extend the construction timeline.
Average timeframe for warehouse construction
The average timeframe for constructing a warehouse significantly depends on various factors, including the project’s size, complexity, and unforeseen challenges. It is crucial for cost-conscious buyers to understand this before embarking on any construction project.
Phase | Average Timeframe | Explanation |
---|---|---|
Initiation | 1-2 weeks | During this phase, project scope and objectives are defined. |
Pre-Construction | 1-2 months | This phase involves securing permits, finalizing designs, and hiring contractors. |
Procurement | 1-3 months | Materials are sourced and purchased during this time, and delivery timelines can influence the overall timeframe. |
Construction Stage | 4-8 months | Actual building of the warehouse takes the longest time. Factors such as the size of the warehouse and weather conditions can influence the duration. |
Post-Construction | 1-2 months | Final inspections, installations, and project close-out processes are conducted in this phase. |
Given these factors, the average timeframe for constructing a typical warehouse can range anywhere between 8-15 months. This timeframe can extend in case of a larger warehouse, as per the ninth important fact that indicates that the cost per square foot can vary by city. It’s crucial for cost-conscious buyers to factor in these timeframes when planning their warehouse construction projects.
Conclusion
In conclusion, estimating the cost of building a warehouse involves considering factors such as size, type, design, materials, and location. By controlling construction costs through efficient design choices and implementing measures like natural light and voice-enabling technology, expenses can be minimized.
It’s important to research specific prices for your city before embarking on a warehouse construction project. Overall, with careful planning and budgeting, you can estimate the cost of building a warehouse and make informed decisions about your investment.
FAQs
1. What is the cost to build a warehouse?
The cost to build a warehouse can change based on many things. This includes factors like shell building or turnkey costs, and other expenses.
2. How do we estimate the expense for warehouse construction?
Cost estimation for warehouse construction uses analysis of past projects and market prices to give an idea about the total budget needed.
3. Can you explain what ‘warehouse development expenses’ are?
Warehouse development expenses cover all money spent in creating a new warehouse, from start to finish. It helps in estimating overall building costs.
4. What affects the price of building a warehouse?
There are many factors that affect the cost. Things such as land price, design, materials used, work force pay and time taken can all alter how much it costs.
5. Is there a way I can calculate my own construction expenses?
Yes! You can use an online tool or software that calculates warehouse construction expenses by looking at your inputs such as size, location, material preferences etc., this will help with planning your budget.
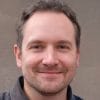
Hi, my name’s David. I started this pricing blog as a side project to help people figure out the best prices on common services. Whether you’re trying to figure out how much it costs to get scanning done at Staples or the expense to bleach short hair, more than likely I’ve blogged about it. Shoot me an email if you have any questions: david@mightyprice.com.